A research team has successfully constructed a glassy Li-ion conduction network and developed amorphous tantalum chloride solid electrolytes (SEs) with high li ion customized battery packs conductivity.
The research results were published in the Journal of the American Chemical Society.
The study shows that compared with ceramic SEs, amorphous SEs distinguish themselves by their inherent unique glassy networks for intimate solid-solid contact and extraordinary li ion customized battery packs conduction percolation.
In addition, amorphous SEs are conducive to fast li ion customized battery packs conduction and are promising for realizing the effective use of high-capacity cathodes and stable cycling; thus, they significantly increase the energy density of all-solid-state lithium batteries (ASSLBs).
However, due to the low areal capacity of the thin-film cathode and the poor room-temperature ionic conductivity, the amorphous Li-ion conduction phosphorous oxynitride (Li1.9PO3.3N0.5, LiPON) is inferior to the current commercialized Li-ion batteries in terms of the energy/power density.
To overcome this challenge, it is necessary to develop amorphous SEs with high Li-ion conductivity and ideal chemical (or electrochemical) stability. It has been revealed that crystalline halides, compounds in which the halogens are negatively valenced, including fluorides, chlorides, bromides, and iodides, are promising to realize high-energy-density ASSLBs for their high voltage stability and high ionic conductivity. However, there are still few studies on developing amorphous chloride SEs.
Researchers proposed a new class of amorphous chloride SEs with high Li-ion conductivity, demonstrating excellent compatibility for high-nickel cathodes, and realized a high-energy-density ASSLB with a wide range of temperatures and stable cycling.
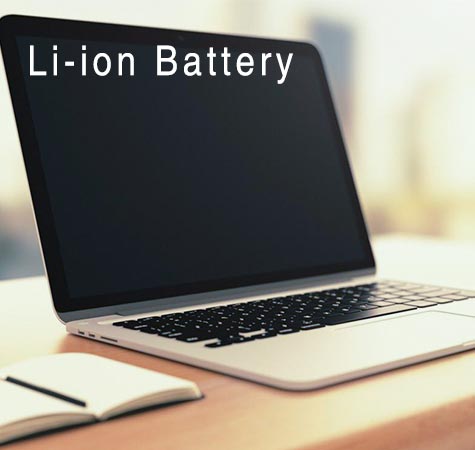
The researchers determined the structural features of the LiTaCl6 amorphous matrix by employing random surface walking global optimization combined with a global neural network potential (SSW-NN) function for a full-situ energy surface search and one-dimensional solid-state nuclear magnetic resonance lithium spectroscopy for the decoupling of chemical environments, X-ray absorption fine-structure fitting, and low-temperature transmission electron microscopy for the microstructural characterization of the matrix.
Based on the flexibility of its component design, a series of high-performance and cost-effective Li-ion composite solid electrolyte materials with the highest room-temperature Li-ion conductivity up to 7 mS cm-1 were further prepared, which meets the practical application requirements of high-magnification ASSLBs.
Furthermore, researchers verified the applicability of the ASSLBs constructed based on amorphous chloride over a wide temperature range: i.e., it can achieve a high rate (3.4 C) close to 10,000 cycles of stable operation in a freezing environment of -10°C. The component flexibility, fast ionic conductivity, and excellent chemical and electrochemical stability exhibited by the amorphous chloride SEs provide new ideas for further designing new SEs and constructing high-ratio ASSLBs.
This breakthrough extends a series of high-performance composite SEs, overcomes the limitations of the structure and component design of traditional crystalline SEs, and paves the way for realizing high-nickel cathodes with high performance for ASSLBs.
The research team was led by Prof. Yao Hongbin from the University of Science and Technology of China (USTC), in collaboration with Prof. Shang Cheng from Fudan University and Prof. Tao Xinyong at Zhejiang University of Technology.
More information: Feng Li et al, Amorphous Chloride Solid Electrolytes with High Li-Ion Conductivity for Stable Cycling of All-Solid-State High-Nickel Cathodes, Journal of the American Chemical Society (2023). DOI: 10.1021/jacs.3c10602
Journal information: Journal of the American Chemical Society
If you have any question, please feel free to contact us:
- Name: Dawn Zeng (Director)
- E-mail address: sales@himaxelectronics.com