A green industrial future for Europe may depend on an element that is part of a household staple: table salt. Dr. John Abou-Rjeily, a researcher at Tiamat Energy in France, is using sodium to develop rechargeable batteries. Sodium is a part of sodium chloride, an ionic compound that is the technical name for ordinary salt.
The idea behind sodium-ion batteries is to reduce Europe’s reliance on the lithium-ion ones that power everything from toothbrushes and mobile phones to mopeds and cars.
Today’s batteries include materials such as lithium, nickel and cobalt that are both scarce and toxic, whereas sodium is one of the most plentiful elements on Earth.
“Sodium-ion batteries are based on more abundant and safer materials than lithium-ion batteries,” said Abou-Rjeily. “There’s not enough lithium ions and cobalt and nickel to meet everyone’s needs.”
He is a research and development engineer at Tiamat, which designs and manufactures sodium-ion batteries.
Abou-Rjeily led a research project to develop sodium-ion batteries that have commercial appeal and can serve as a new foundation for European manufacturing.
Called NAIMA, the project ran from December 2019 through May 2023. It featured companies, research institutions and universities in Bulgaria, Belgium, France, Germany, the Netherlands, Slovenia, Spain and Sweden.
Battery charge
Batteries are central to Europe’s drive to replace fossil fuels with renewable-energy sources such as wind and solar power. More clean energy in Europe requires new storage capacity that batteries can provide.
The European battery market could be worth as much as €250 billion a year as of 2025. Europe aims to increase its share of global battery-cell production to as high as 25% this decade from 3% in 2018, chipping away at Asia’s 85% dominance.
The research covers all segments of the supply chain—from access to raw materials needed to make batteries and the infrastructure required for storing energy to “smart grids” that automatically charge vehicles when power is cheapest and battery designs that ensure recycling.
Lithium-ion batteries can store lots of energy in a small space, making them winners for smart phones and electric cars. Sodium-ion batteries are slightly bigger and potentially cheaper, making them candidates for storing energy in places such as homes, power tools and small vehicles.
French connection
Abou-Rjeily, a trained chemist from Lebanon, moved to France in 2016 to pursue an interest in environmental sustainability.
He is at home with Tiamat, whose sodium-ion batteries exclude lithium, cobalt and copper and largely avoid nickel too. The company is a spinoff from the French National Center for Scientific Research, or CNRS, which was among the NAIMA participants.
Lithium, cobalt, copper and nickel are on an EU list of critical raw materials, highlighting concerns in Europe about reliance on foreign suppliers and supply squeezes.
For example, when it comes to lithium-ion batteries worldwide, China manufactured almost 80% of them in 2021.
Furthermore, most global production of lithium-ion batteries is expected to go to the automotive industry.
Tiamat plans in 2026 to open a gigafactory in the French city of Amiens to produce sodium-ion batteries suitable initially for equipment such as power tools, according to Abou-Rjeily.
He said NAIMA helped advance the company’s battery know-how.
https://youtu.be/ojLGPk4UltE
The project also helped partners move forward with a type of sodium-ion battery for renewable-energy storage. This kind of battery could also one day be suitable for some cars.
While it wouldn’t ever challenge the 500-kilometer capacity of lithium-ion batteries, this sodium-ion type could be more competitive for smaller stretches, according to Abou-Rjeily.
“They could be cheaper for short and medium driving distances,” he said.
Home base
An energy link between cars and homes through sodium-ion batteries is a vision of Dr. Magdalena Graczyk-Zajac, a visiting professor at the Technical University Darmstadt in Germany.
Also an electrochemist at the German energy company EnBW, she is involved in a project to develop a sodium-ion battery for homes. Called SIMBA, the project is due to wrap up in June 2024 after three and a half years.
Graczyk-Zajac paints a future where energy captured by photovoltaic panels on homes is stored in a rechargeable household sodium-ion battery. The battery would then power the homes and charge the inhabitants’ electric vehicles.
Graczyk-Zajac said such a scenario would mean a big cut in transportation costs.
“You could be driving your car for free for eight to nine months of the year,” she said.
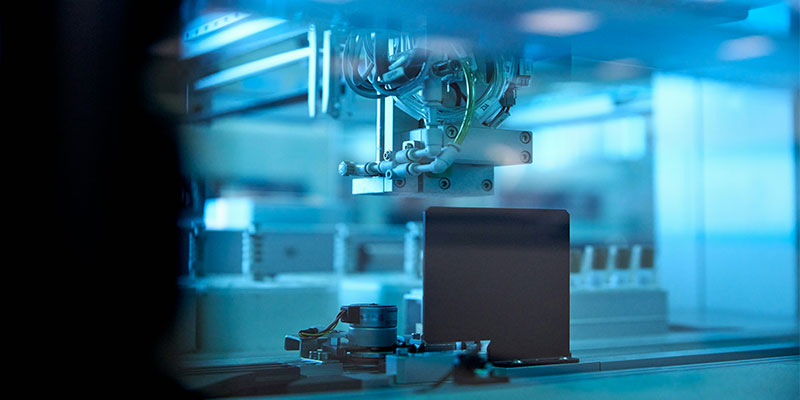
Household gains
While sodium-ion and lithium batteries work in a similar way, sodium is a larger ion than lithium. That’s one reason that a sodium-ion battery takes up a little more space.
For home storage, such a battery would be placed underground or in a garage, so a slightly larger battery wouldn’t matter much, according to Graczyk-Zajac.
SIMBA, which involves almost 20 research institutes, universities and companies from across Europe, has put together some essential components of a home sodium-ion battery for laboratory testing.
One part, the anode, is made from hard carbon, which can be manufactured from wood or biowaste. Another—the cathode—can be made of a material called Prussian white.
While lithium-ion cathodes frequently contain cobalt, this Prussian white cathode contains iron, which is a more abundant and cheaper metal.
This cathode was developed by Altris, a spinoff in 2017 from Uppsala University in Sweden—one of the SIMBA participants.
Altris made headlines in November 2023 when its industry partner, Sweden-based Northvolt, announced that it would make batteries in Europe with the cathode.
In general, sodium-ion batteries promise households in Europe the chance for cheaper and cleaner energy.
The batteries also offer the prospect of financial gains through the storage and then either sale of spare electricity to the grid when home production is higher than needed or later use in the home.
Graczyk-Zajac recommends the later-use option. “A householder would save more money by just keeping that energy,” she said.
More information:
- NAIMA
- SIMBA
- EU energy research and innovation
- European Battery Alliance
Provided by Horizon: The EU Research & Innovation Magazine