As electric vehicle (EV) demand accelerates, so does the need for lithium batteries. But these batteries contain valuable critical minerals, as well as toxic materials, so they should not be treated as common waste.
Unlike China and some European countries, Australia lacks a dedicated lithium battery recycling facility. Just 10% of Australia’s lithium battery waste was “recycled” in 2021. This means the batteries were collected and shredded locally before being sent overseas for recycling.
Shipping large volumes of spent batteries overseas is complex and risky. Lithium batteries have been known to start fires. A cargo ship laden with lithium batteries caught fire off the coast of Alaska in December 2023. The fire burned for days.
Similarly, a fire broke out on a cargo ship carrying luxury vehicles (including EVs) near Portugal’s Azores Islands in February 2022. The risk of fire is even greater for spent EV batteries because they are more likely to be damaged or unsafe.
Efforts to recycle batteries onshore have now been jeopardized by the decision—announced last week ahead of this week’s federal budget—to scrap plans for a waste export levy. The proposed A$4 per ton levy on waste exports would have come into effect on July 1.
Scrapping the levy will pave the way for even more waste to be exported rather than recycled here. We believe there should be exceptions for spent lithium batteries—for several reasons. These include safety concerns around shipping and the loss of critical minerals.
By recycling onshore, we can retain these resources, build new industries and develop a circular economy. We should also prepare for the possibility that other countries will at some stage refuse to accept our waste. Then we will be forced to stockpile these batteries, at great risk.
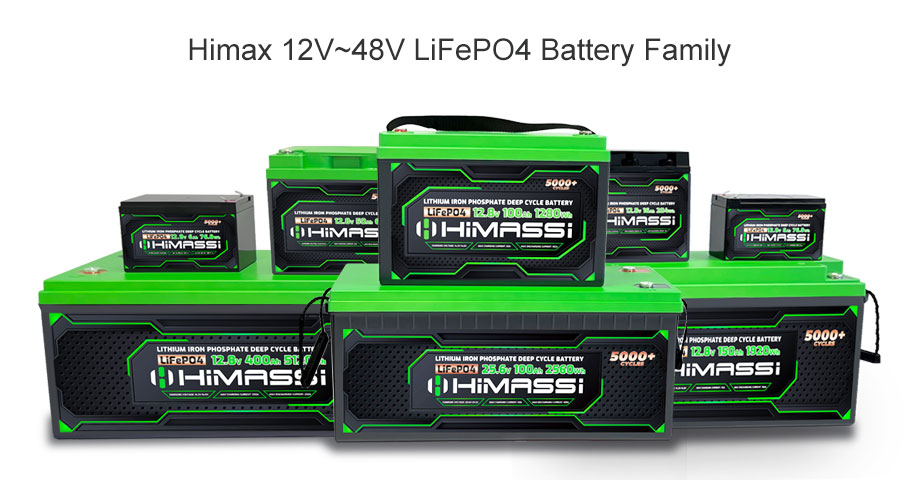
Spent EV batteries are accumulating rapidly
EV sales are growing exponentially. Globally, one in five new cars are electric. More than half of all cars sold by 2040 will likely be EVs.
Beneath each sleek exterior is a hefty lithium battery with an average lifespan of just five to eight years.
According to the International Energy Agency, EVs generated about 500,000 tons of battery waste in 2019 alone. This waste is forecast to reach 8 million tons by 2040.
A 2016 report for the federal government forecasts at least 20% annual growth in Australian lithium battery waste to 136,000 tons a year by 2036.
CSIRO explored the potential for lithium battery recycling and reuse in 2021. But little has happened since.
Meanwhile, the mountain of waste continues to grow. It is estimated 360,000 tons of EV batteries will be spent by 2040 and 1.6 million tons by 2050.
Battery recycling is a must, not a choice
Disposal of lithium batteries can cause fires and explosions in waste management facilities and landfills. If a battery is punctured, or short-circuits, the residual electricity can spark fires or explode. The batteries can also leak metals such as cobalt, nickel or manganese, threatening ecosystems and human health.
The battery fluid is harmful to humans as it is linked to various health effects including heart attacks, asthma, cancer, eye damage, reproductive toxicity, skin sensitisation, damage to bones and kidneys and other symptoms.
Lithium battery wastes are overground mines
Rather than being seen as a liability, the growing pile of spent lithium batteries could represent an economic opportunity for Australia. The battery pack in a BMW i3 electric vehicle, for example, contains 6kg of lithium, 35kg of graphite, 2kg of cobalt, 12kg of nickel and 12kg of manganese. These valuable resources will be wasted if the batteries are exported or sent to landfill.
If the raw materials were instead recovered and processed onshore, this could translate into a burgeoning industry worth A$3.1 billion, using Australia’s existing expertise in mining and resource recovery.
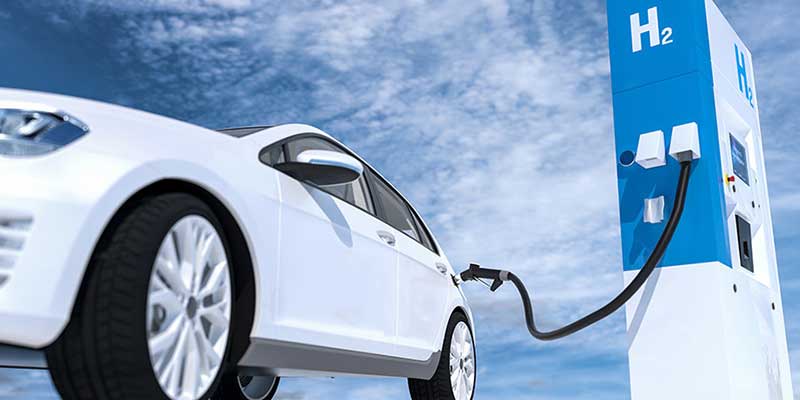
It’s time to get serious about battery recycling
The federal government missed an opportunity to include infrastructure for battery recycling in its A$250 million Recycling Modernisation Fund. These funds were limited to waste glass, plastic, tires, paper and cardboard.
This delays the establishment of onshore capacity for battery recycling and makes us reliant on exporting waste batteries overseas.
To boost recycling, we must develop clear regulations and guidelines aligned with global standards, including stringent restrictions on landfill.
In addition, incentives such as tax credits and rebates for battery recycling programs will encourage investment in this area and drive progress. Such measures in Europe make the legislated target for lithium recovery from waste batteries (63% by 2027) possible, cutting reliance on imports of raw materials.
We urgently need to develop a comprehensive waste management strategy dedicated to the responsible collection and recycling of waste batteries. Such a strategy is crucial to safeguard both the environment and communities from the potential hazards associated with improper disposal, promoting resource conservation and creating a circular economy for these critical energy storage devices.
Provided by The Conversation
This article is republished from The Conversation under a Creative Commons license. Read the original article.