Custom lithium battery pack innovation is not easy.
In the past decade or so, Custom lithium battery pack industrialization has developed rapidly and production capacity has increased by leaps and bounds. However, there have been few revolutionary breakthroughs in lithium battery technology.
In terms of material system, lithium iron phosphate and ternary are still dominant; in terms of structural system, square, cylindrical and soft packages are still dominant.
In the final analysis, there are many constraints on lithium battery innovation, and factors such as cost, safety, energy density, cycle times, temperature performance and even resource security need to be taken into consideration at the same time.
In the context of difficult innovation, the lithium battery industry has also carried out various explorations in recent years, including cobalt-free, high-nickel, solid-state, composite current collectors, lithium iron manganese phosphate and even sodium-ion batteries that are free of lithium resources in terms of material systems. Short knives, blades, 4680 large cylinders, and high-speed lamination from manufacturing process angles, etc.
Regarding the mature material system and structural system, from the perspective of industrialization, penetration rate and industrial impact, among the technological innovations in recent years, which technical route is more prominent? Who can be called the second technical line?
This is a topic worth taking stock of.
What is The second technical route?
Comprehensive comparison shows that lamination technology innovation is more prominent.
The lamination process has the characteristics of higher energy density, more stable internal structure, longer cycle life, and safer. It is not only very suitable for long and thin battery cells, but also has a higher degree of compatibility with large-capacity battery cells.
The winding process that once dominated the mainstream has many bending areas and current collector welding areas, low internal space utilization, and uneven winding tension and deformation, especially in long thin and large capacity applications. The disadvantages are more obvious under the trend.
In recent years, Honeycomb Energy has taken the lead in applying lamination technology to square batteries, replacing the winding process and solving the problem of low efficiency of traditional lamination equipment. High-speed lamination technology has been continuously iterated for 3 generations, with efficiency and yield rates continuously improving, and costs increasing. The “flying stack” speed of the third-generation technology has reached 0.125 seconds/piece, achieving the same efficiency as the winding process.
Lamination technology has also encountered a “historic opportunity”. With the rapid development of power batteries and energy storage batteries, the requirements for prismatic batteries and blade batteries are constantly increasing. The advantages of lamination technology in supporting and promoting the innovation of prismatic batteries and blade batteries are also increasing. It’s becoming more and more obvious.
As a leader and staunch supporter of lamination technology, Honeycomb Energy has fully adopted lamination technology since the company was founded. As of the end of 2022, the production capacity of the lamination process has reached 15.6GWh, and it is mainly high-speed lamination. It will continue to expand with the implementation of planned production capacity.
Nowadays, lamination technology is accelerating its promotion and fully penetrated.
At present, the leading lithium battery companies have adopted lamination technology to varying degrees and have all entered the market. Especially in large-capacity square, blade and soft-pack batteries, lamination technology has become a trend or even a must.
Judging from the results, compared with other technological innovations in recent years, the innovative iteration and industrialization effect of lamination technology are more prominent. Leading companies have made plans one after another, and the penetration rate continues to increase.
Custom lithium battery pack innovation is “blooming”. From the perspective of industrialization and penetration, the lamination technology that is constantly iterating in process innovation has opened up a new world beyond traditional winding technology and has become the well-deserved “second technology route” of lithium battery. .
The platform effect of stacking technology is prominent
Stack technology is more like a process platform.
On this platform, it is compatible with different material systems such as ternary, lithium iron phosphate and even solid-state batteries and semi-solid batteries, as well as different structural systems such as square, blade and soft pack.
Therefore, lamination technology has a strong industrial amplification effect and is of great value in promoting the technological progress and industrial development of the lithium battery industry.
Especially in the blade battery, it can be said to be a “perfect match” and “mutual achievement” with the lamination technology. Without the lamination technology, it would be difficult for the “long and thin” blade battery to shine. After all, the winding technology has “winding technology”. “around” the limit.
The same is true not only for blade batteries, but also for prismatic batteries, especially larger models. With the development of the energy storage industry, prismatic batteries continue to “expand”, from the previously popular 280Ah to today’s 300Ah+, lamination technology can support the larger size of prismatic batteries.
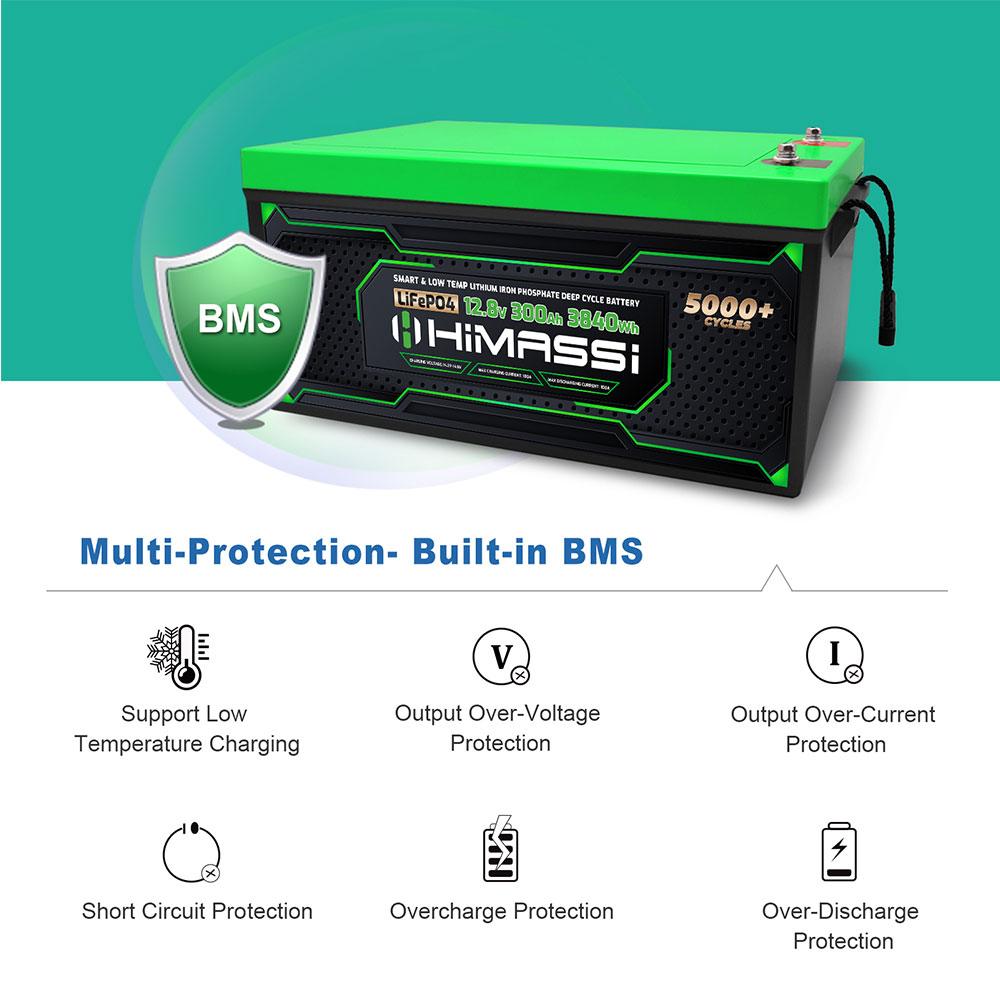
For soft-pack batteries, lamination technology is a natural “perfect match” and can bring greater packaging advantages, especially when combined with emerging semi-solid-state batteries and solid-state batteries, the advantages are even more obvious.
Lamination technology has stimulated innovation at the cell level in large-capacity prismatic batteries, blade batteries, and soft-pack batteries. It is also very helpful in promoting innovation in battery packs. Even CTP and CTC can achieve better integration effects at the system level.
As a platform technology, lamination technology has brought lithium battery structural innovation to a new level, inspiring innovation at the prismatic battery, blade battery, pouch battery and even battery system level, leading the innovation of a new generation of lithium battery technology, with huge flexibility, the industry has far-reaching impact.
If you have any question, please feel free to contact us:
- Name: Dawn Zeng (Director)
- E-mail address: sales@himaxelectronics.com