A green battery revolution
What if a common element, rather than scarce expensive ones, was a key component in electric car batteries? A collaboration co-led by an Oregon State University chemistry researcher is hoping to spark a green battery revolution by showing that iron instead of cobalt and nickel can be used as a cathode material in lithium-ion batteries.
Multiple reasons of the important findings
The findings, published in Science Advances, are important for multiple reasons, Oregon State’s Xiulei “David” Ji notes.
“We’ve transformed the reactivity of iron metal, the cheapest metal commodity,” he said. “Our electrode can offer a higher energy density than the state-of-the-art cathode materials in electric vehicles. And since we use iron, whose cost can be less than a dollar per kilogram—a small fraction of nickel and cobalt, which are indispensable in current high-energy lithium-ion batteries—the cost of our batteries is potentially much lower.”
At present, the cathode represents 50% of the cost in making a lithium-ion battery cell, Ji said. Beyond economics, iron-based cathodes would allow for greater safety and sustainability, he added.
As more and more lithium-ion batteries are manufactured to electrify the transportation sector, global demand for nickel and cobalt has soared. Ji points out that in a matter of a couple of decades, predicted shortages in nickel and cobalt will put the brakes on battery production as it’s currently done.
In addition, those elements’ energy density is already being extended to its ceiling level—if it were pushed further, oxygen released during charging could cause batteries to ignite—plus cobalt is toxic, meaning it can contaminate ecosystems and water sources if it leaches out of landfills.
Put it all together, Ji said, and it’s easy to understand the global quest for new, more sustainable battery chemistries.

The basic work way and basic components of batteries
A battery stores power in the form of chemical energy and through reactions converts it to the electrical energy needed to power vehicles as well as cellphones, laptops and many other devices and machines. There are multiple types of batteries, but most of them work the same basic way and contain the same basic components.
A battery consists of two electrodes—the anode and cathode, typically made of different materials—as well as a separator and electrolyte, a chemical medium that allows for the flow of electrical charge. During battery discharge, electrons flow from the anode into an external circuit and then collect at the cathode.
In a lithium-ion battery, as its name suggests, a charge is carried via lithium ions as they move through the electrolyte from the anode to the cathode during discharge, and back again during recharging.
Effective utilization of resources
“Our iron-based cathode will not be limited by a shortage of resources,” said Ji, explaining that iron, in addition to being the most common element on Earth as measured by mass, is the fourth-most abundant element in the Earth’s crust. “We will not run out of iron ’til the sun turns into a red giant.”
Ji and collaborators from multiple universities and national laboratories increased the reactivity of iron in their cathode by designing a chemical environment based on a blend of fluorine and phosphate anions—ions that are negatively charged.
The blend, thoroughly mixed as a solid solution, allows for the reversible conversion—meaning the battery can be recharged—of a fine mixture of iron powder, lithium fluoride and lithium phosphate into iron salts.
“We’ve demonstrated that the materials design with anions can break the ceiling of energy density for batteries that are more sustainable and cost less,” Ji said.
“We’re not using some more expensive salt in conjunction with iron—just those the battery industry has been using and then iron powder. To put this new cathode in applications, one needs to change nothing else—no new anodes, no new production lines, no new design of the battery. We are just replacing one thing, the cathode.”
Storage efficiency still needs to be improved, Ji said. Right now, not all of the electricity put into the battery during charging is available for use upon discharge. When those improvements are made, and Ji expects they will be, the result will be a battery that works much better than ones currently in use while costing less and being greener.
“If there is investment in this technology, it shouldn’t take long for it to be commercially available,” Ji said. “We need the visionaries of the industry to allocate resources to this emerging field. The world can have a cathode industry based on a metal that’s almost free compared to cobalt and nickel. And while you have to work really hard to recycle cobalt and nickel, you don’t even have to recycle iron—it just turns into rust if you let it go.”
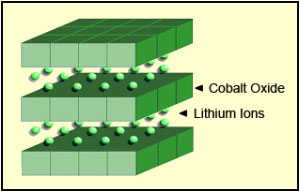
Contribution of the research
The research was co-led by Tongchao Liu of Argonne National Laboratory and included Oregon State’s Mingliang Yu, Min Soo Jung and Sean Sandstrom.
Scientists from Vanderbilt University, Stanford University, the University of Maryland, Lawrence Berkeley National Laboratory and the SLAC National Accelerator Laboratory also contributed.
More information: Mingliang Yu et al, Unlocking Iron Metal as a Cathode for Sustainable Li-ion Batteries by an Anion Solid-Solution, Science Advances (2024). DOI: 10.1126/sciadv.adn4441. www.science.org/doi/10.1126/sciadv.adn4441
Journal information: Science Advances