Can LiFePO4 Batteries Be Mounted on Their Side? Exploring Installation Flexibility
LiFePO4 (lithium iron phosphate) batteries are well-regarded for their robustness, long life span, and safety features. A common question that arises with the use of these batteries in various applications is regarding their mounting flexibility—specifically, whether they can be installed on their side without compromising performance or safety. This article provides a thorough exploration of this topic, supported by insights into how Himax Electronics designs versatile battery solutions.
Understanding LiFePO4 Battery Design
Before delving into the orientation specifics, it’s essential to understand the basic design and construction of LiFePO4 batteries:
- Cell Structure: LiFePO4 batteries are typically made up of cells containing a cathode, an anode, a separator, and an electrolyte. The cells can be enclosed in different formats such as cylindrical, prismatic, or pouch cells, each offering unique benefits and considerations regarding spatial configuration.
- Electrolyte and Sealing Technology: Unlike traditional liquid electrolyte-based batteries, LiFePO4 batteries usually use a stable solid or gel-type electrolyte that minimizes leakage risks. The cells are sealed tightly to prevent any exposure of the electrolyte to the external environment.
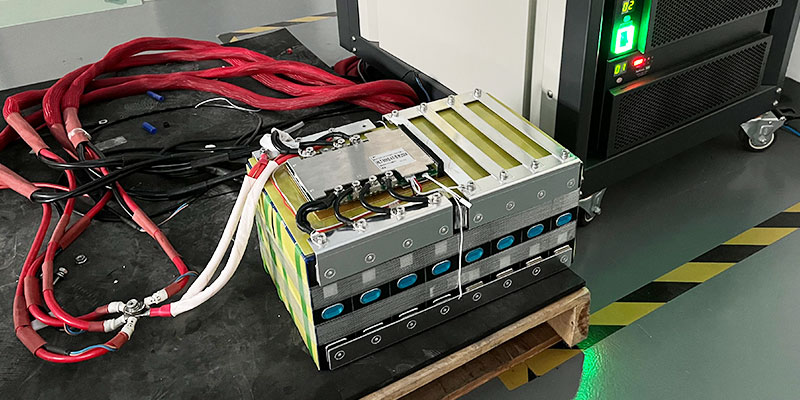
Can LiFePO4 Batteries Be Mounted on Their Side?
The answer largely depends on the specific battery design and its internal construction, but here are general considerations:
- Leakage and Venting: Since LiFePO4 batteries generally use non-liquid electrolytes, there is minimal risk of leakage when mounted sideways. Moreover, the venting mechanisms are designed to operate effectively irrespective of the battery’s orientation.
- Mechanical Stability: The robust internal structure of LiFePO4 batteries allows them to withstand various mounting positions. The mechanical stability is ensured by the sturdy casing and the secure arrangement of internal components, making side mounting a viable option.
- Thermal Management: One of the crucial aspects of battery installation is ensuring proper thermal management. LiFePO4 batteries, known for their thermal stability, maintain consistent performance across different orientations, including when mounted on their side.
Application-Specific Considerations
While LiFePO4 batteries offer flexibility in mounting, certain applications may have specific requirements or best practices:
- Electric Vehicles and Marine Applications: In EVs and boats, space optimization is crucial. LiFePO4 batteries are often mounted on their side to fit into specific design layouts without compromising safety or efficiency.
- Energy Storage Systems: For stationary applications like solar energy storage, batteries can be installed in various configurations, including vertically or horizontally, to best utilize the available space and facilitate maintenance and ventilation.
- Portable and Backup Power: In portable power packs and UPS systems, LiFePO4 batteries are designed to be highly versatile in terms of installation, supporting various orientations to adapt to different space constraints and usage requirements.
Himax Electronics: Enhancing Flexibility and Safety in Battery Installations
Himax Electronics is at the forefront of developing LiFePO4 battery technologies that support diverse application needs, including flexible mounting options:
- Innovative Design Solutions: Himax designs batteries with advanced casing and internal support structures that allow for multiple mounting positions without compromising the integrity or performance of the battery.
- Customized Battery Systems: Understanding that different applications have unique needs, Himax offers customized battery solutions that consider mounting flexibility as a critical design parameter.
- Safety and Reliability: With a commitment to safety, Himax ensures that all battery products, regardless of their intended orientation, meet rigorous safety standards. This includes extensive testing for shock, vibration, and thermal performance to guarantee reliability in various mounting scenarios.
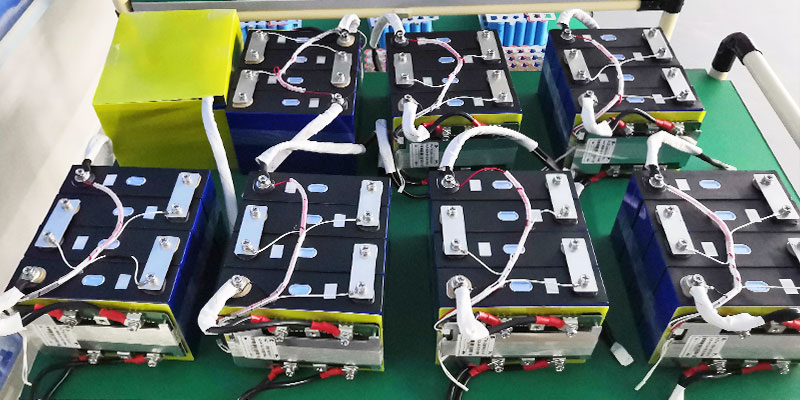
Conclusion
LiFePO4 batteries can indeed be mounted on their side, thanks to their advanced design and construction that prevent leakage and ensure stable performance in various orientations. Whether for vehicular applications, stationary storage, or portable power, these batteries provide the flexibility needed for efficient space management and installation ease.
Himax Electronics continues to lead in providing versatile, safe, and efficient LiFePO4 battery solutions, supporting a wide range of industries and applications with innovative energy storage technologies. For more information on LiFePO4 batteries and custom solutions tailored to your needs, visit Himax Electronics or contact their technical support team.