As a professional battery manufacturer with over 12 years of experience, HIMAX specializes in the design and production of high-quality rechargeable batteries, including Li-ion, LiFePO4, NiMH, and especially Lithium Polymer (LiPo) batteries. Our factory is equipped with advanced production lines, automatic welding machines, and aging test equipment to ensure every battery meets the highest standards. In this article, we focus on LiPo batteries and their applications in wearable lighting devices, such as LED wristbands for concerts, wearable flashlights, headlamps, and hunting lamps.
Why LiPo Batteries Are Ideal for Wearable Lighting Devices
Key Benefits of LiPo Batteries in Wearable Technology
1. Compact and Flexible Form Factor
LiPo batteries offer flexible design possibilities due to their slim and compact structure, making them ideal for space-constrained applications like wristbands or headlamps. Unlike cylindrical batteries, LiPo cells can be manufactured in various shapes and sizes to fit customized designs.
2. High Energy Density
These batteries provide a higher energy-to-weight ratio, which means more power can be packed into a lighter battery—critical for comfort and portability in wearable devices.
3. Rechargeable and Long Cycle Life
All our LiPo batteries are rechargeable and designed to offer 300+ charge cycles, ensuring long-lasting performance and minimizing electronic waste.
4. High Safety Standards
Our batteries are equipped with overcharge, over-discharge, and short-circuit protection, meeting international safety standards. For wearable devices, safety is paramount as the battery is in close contact with the user’s body.
5. Reliable Performance in Various Conditions
Our factory ensures every batch of batteries undergoes rigorous aging and stress testing, making them suitable for both indoor and outdoor lighting wearables.
Recommended LiPo Battery Models for Wearable Lighting Devices
We supply a range of LiPo battery models suitable for different wearable lighting applications. Below is a comparison of some of our best-selling models:
Model | Voltage (V) | Capacity (mAh) | Dimensions (mm) | Ideal Applications |
503738 | 3.85 | 830 | 5.0 x 37 x 38 | LED wristbands, slim wearable flashlights |
633650 | 3.7 | 1200 | 6.3 x 36 x 50 | Wearable flashlights, compact headlamps |
603035 | 3.7 | 1200 | 6.0 x 30 x 35 | LED armbands, wearable safety lights |
854169 | 3.7 | 2600 | 8.5 x 41 x 69 | High-capacity hunting lamps, headlamps |
903450 | 3.85 | 2250 | 9.0 x 34 x 50 | Outdoor wearables, long-runtime headlamps |
Applications of LiPo Batteries in Wearable Lighting
Common Use Cases
LED Concert Wristbands: Require ultra-light, compact batteries for hours of illumination during live performances.
Wearable Flashlights: Designed for hand-free use, needing high-energy compact batteries.
Headlamps and Helmet Lights: Require long-runtime and stable output for outdoor activities.
Hunting Lights: Need robust, long-lasting, and powerful battery packs for field use.
Why Choose Us as Your Battery Partner
As a LiPo battery factory with in-house R&D and manufacturing, we ensure:
Direct factory pricing: Eliminate intermediaries, save costs and create higher profits for you
Custom battery pack design support: Professional customization service, customized batteries according to your project requirements
Fast lead time and global shipping: Mature production line + long-term cooperative freight forwarder, providing stable production delivery and transportation services
Strict quality control and certification: (RoHS, CE, UN38.3, MSDS)
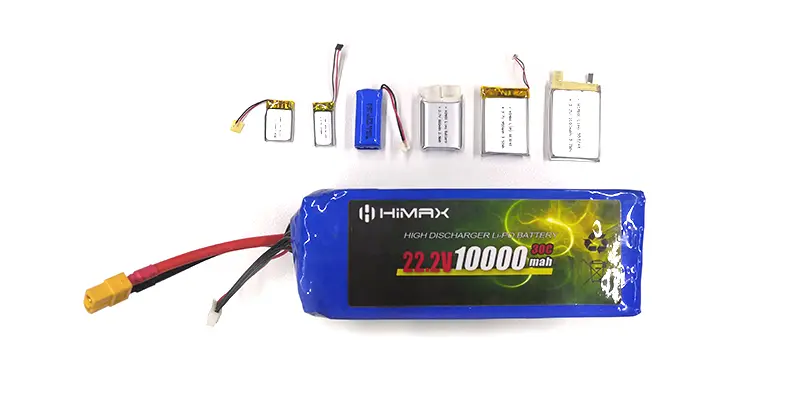
custom lipo battery packs
Conclusion
Lithium Polymer batteries have proven to be the best power solution for wearable lighting devices due to their compact size, high capacity, and safety features. Our factory offers a complete range of LiPo battery models ideal for various wearable applications, supported by expert production capabilities and strict quality standards.
If you are looking for a reliable LiPo battery supplier for your wearable lighting products, feel free to contact us for samples or custom solutions.