Tesla’s 4680 lithium-ion battery refers to a battery with a diameter of 46 mm and a height of 80 mm. The battery currently uses the ternary lithium battery technology route, and it is not ruled out that lithium iron phosphate batteries will be launched in the future. Its shape is cylindrical, which is different from the mainstream square battery.
Its main features and advantages and disadvantages are as follows:
High energy density: Tesla’s battery uses a larger battery size and a new design to provide higher energy density, making the battery capacity larger, thereby extending the range of electric vehicles.
Improved heat dissipation performance: The 4680 battery adopts an irregular surface design to improve the heat dissipation effect, making the battery temperature rise more gentle during high-power discharge, and improving the battery’s service life and safety.
Higher charging rate: The 4680 battery has a higher charging rate, can charge faster, and shortens the charging time.
Reduce costs: The 4680 battery uses a new production process, including the use of fewer parts and a more efficient production line, which is expected to reduce production costs and drive down the price of electric vehicles.
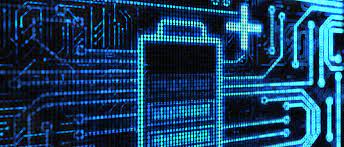
Disadvantages of the 4680 lithium battery:
Technology novelty: As it is a brand-new battery design, the technology of the 4680 lithium-ion battery is relatively new, and there may be technical immaturity and reliability risks.
Production scale and supply chain: Large-scale production of 4680 lithium-ion batteries may require adjustments to Tesla’s production equipment and supply chain, and there may be challenges such as insufficient supply in the short term.
Cost and investment: Although the 4680 lithium-ion battery is expected to reduce production costs, new production processes and equipment may require a large investment.
At present, the 4680 lithium battery is not mature enough in terms of technology, especially the pole-free design requires high welding technology. In addition, the 4680 lithium battery also faces challenges in heat dissipation because they are too large and are not as good as small-sized cylindrical or sheet cells in radial heat dissipation.