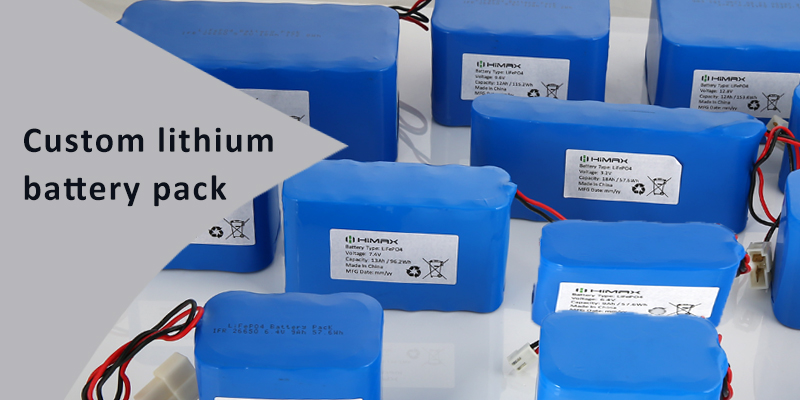
Basic Characteristics of 18650 Battery Cells
Size and Specifications
The 18650 battery cell is a standardized lithium-ion battery, named after its dimensions: 18mm in diameter and 65mm in length. This specification has become a mainstream choice in the lithium battery market due to its mature production process and wide range of applications.
Voltage and Capacity
A single 18650 battery cell has a standard voltage of 3.7V and a capacity typically ranging from 2000mAh to 3500mAh. By combining multiple cells in series and parallel, different voltage and capacity requirements can be achieved. For example, 10 cells in series can achieve 37V, while parallel connections can increase the total capacity.
Chemical Composition
The chemical composition of 18650 battery cells includes cathode materials (such as ternary lithium or lithium iron phosphate), anode materials (such as graphite), electrolytes, and separators. Different chemical formulations affect battery performance, including energy density, cycle life, and safety.
Advantages of 18650 Battery Cells in 7.4V 4400mAh Applications
The 18650 battery cell, with its standardized design, high performance, and mature production process, is an ideal solution for 7.4V 4400mAh lithium-ion batteries. Below, we analyze its advantages in terms of voltage matching, capacity optimization, and application scenarios.
Voltage Matching
A 7.4V voltage is typically achieved by connecting two 18650 battery cells in series. A single cell has a standard voltage of 3.7V, so two cells in series reach 7.4V. This combination is simple, efficient, and meets the needs of most portable devices.
-
Advantages of Series Design: Series design not only increases voltage but also maintains a reasonable size and weight for the battery pack. For example, two 18650 cells in series measure only 36mm in diameter and 65mm in length, making them ideal for space-constrained devices.
-
Voltage Stability: 18650 cells maintain stable voltage output during discharge, which is crucial for devices requiring constant voltage, such as power tools and drones.
Capacity Optimization
A 4400mAh capacity can be achieved in two ways:
1. Parallel Design: Using two 2200mAh cells in parallel achieves a total capacity of 4400mAh. Parallel design increases capacity without raising voltage, making it suitable for devices requiring long runtimes.
2. High-Capacity Cells: Directly using a single 4400mAh high-capacity 18650 cell. This simplifies battery pack design and reduces connection points and failure risks.
-
Advantages of Parallel Design: Parallel design not only increases capacity but also enhances discharge capability. For example, two 2200mAh cells in parallel can double the maximum discharge current, making them suitable for high-power devices.
-
Advantages of High-Capacity Cells: High-capacity cells reduce the size and weight of the battery pack while lowering assembly complexity, making them ideal for applications with strict space and weight requirements.
Application Scenarios
The 7.4V 4400mAh battery pack, with its high performance and flexibility, is widely used in various fields:
-
Drones:
-
Requirements: Drones need high-energy-density batteries to extend flight time while requiring lightweight and compact designs.
-
Solution: The 7.4V 4400mAh battery pack provides sufficient energy support while maintaining a lightweight design, meeting the endurance and performance needs of drones.
-
-
Power Tools:
-
Requirements: Power tools require stable voltage output and high discharge capability to support high-power operation.
-
Solution: The 7.4V 4400mAh battery pack delivers stable voltage and high discharge current, ensuring efficient operation of power tools.
-
-
Portable Medical Devices:
-
Requirements: Portable medical devices need long-lasting batteries that are also safe and reliable.
-
Solution: The 7.4V 4400mAh battery pack offers extended runtime and ensures safety through built-in protection circuits.
-
-
Other Applications:
-
Outdoor Lighting: The 7.4V 4400mAh battery pack provides long-lasting power for outdoor lighting equipment.
-
Portable Audio: High-capacity battery packs extend the playback time of audio devices, enhancing user experience.
-
Future Trends of 18650 Battery Cells
Technological Innovations
With advancements in material science, 18650 battery cells are moving toward higher energy density, longer cycle life, and faster charging speeds. For example, silicon-carbon anode materials can significantly increase capacity, while solid-state electrolytes may improve safety.
Market Demand
As power tools, energy storage systems, and electric vehicles become more popular, the demand for high-performance lithium batteries continues to grow. The 7.4V 4400mAh battery pack, with its balanced performance and cost, is a preferred choice for many applications.
Alternative Technologies
Although 18650 cells currently dominate the market, emerging technologies like solid-state batteries may pose challenges in the future. Solid-state batteries offer higher safety and energy density, but their cost and production processes still need optimization.
The 18650 battery cell, with its standardized design, high performance, and mature production process, is an ideal solution for 7.4V 4400mAh lithium-ion batteries. Through series and parallel configurations, it can flexibly meet the voltage and capacity requirements of various devices. In the future, with continuous technological innovation and growing market demand, 18650 battery cells will continue to play a vital role in the high-performance battery industry.
If you need to customize a 36V 15000mAh lithium battery or other high-performance battery solutions, contact HIMAX Electronics. We offer end-to-end services from design to production, ensuring the highest quality products and technical support. Reach out to us today for more information or a quote!